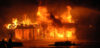
Cheap external cladding materials from China pose fire risk
Article by Landis Michaels, Rebecca Hosking and Gavin Creighton
Some types of cladding materials imported from China fail to comply with Australian standards and lack the fire-retardant qualities of compliant products. The China-Australia Free Trade Agreement (ChAFTA) could exacerbate this problem.
Combustible external cladding allows Docklands fire to spread
In November 2014 the Lacrosse Residential Apartment Building in Docklands, Melbourne caught fire, suffering extensive damage. The fire was sparked by a cigarette on an eighth floor balcony. The building’s combustible external cladding enabled the fire to race up to the 21st floor.
It was subsequently found that the cladding material was imported from China and was not tested to Australian standards. (See Simon King’s article Fire-risk cladding a legal minefield, apartment owners warned, The Australian (online), 5 May 2015.)
Cheaper imported cladding materials fail to meet Australian standards
The use of cladding materials in the last ten years has been widespread due both to the demand for high-rise buildings and to the product’s multifaceted use for insulation, improved rigidity and cosmetic purposes.
The Fire Protection Association Australia has warned that builders across the country are importing Chinese cladding material which has not been tested to Australian standards. The cladding is comprised of a plastic core compressed between aluminium panels and it is the cheaper imported material that is less fire-retardant than compliant products.
Insurers advised to request proof that building materials are compliant
Strata insurers accept in good faith that buildings are being constructed safely, but this may not always be the case. To manage this risk, insurers may consider requesting certified documents to show that the material being used is compliant.
Insurers may also turn their mind to conducting assessments of existing and newly constructed strata buildings to determine the extent of use of cladding or other materials which do not meet Australian standards.
As the defect in the materials is not readily apparent until, for example, a fire ignites, there may be limited or no recourse to the builders, developers and certifiers if they are long gone by the time such an event occurs.
Victorian Building Authority auditing high-rise buildings in inner Melbourne
The Metropolitan Fire Brigade in Melbourne has recently asked the coroner to investigate the root cause of the fire and whether the national and state regulatory frameworks ensure risks are adequately addressed. (See Tom Nightingale’s articleVictorian coroner asked to investigate Docklands high-rise apartment fire involving substandard cladding, ABC News (online), 1 June 2015.)
Further, the Victorian Building Authority (VBA) has recently taken action by commencing an audit of some 170 high-rise buildings in inner Melbourne to ascertain whether there has been non-compliant use of cladding, as well as commencing an investigation into the conduct of the builder and surveyor in relation to the Lacrosse building. (See Lacrosse Docklands fire – VBA to investigate, VBA media release, 27 April 2015.)
The VBA is progressively publishing its findings as these audits are conducted. (See VBA website, Audit of cladding on high rise buildings, 17 June 2015.)
ChAFTA predicted to increase influx of falsely labelled products
Housing Industry Association senior executive director, building development and environment, Kristin Brookfield, recently said that the new free trade agreement with China will result in an increase in products entering the country and without an appropriate checking framework, the current problems stemming from falsely labelled building products will be exacerbated. (See Michael Bleby’s article Dodgy building products could increase under China FTA, industry players warn, The Australian Financial Review (online), 17 June 2015.)
Building professionals, owners, managers and their insurers need to be aware of risks
Body corporates, strata managers and owner organisations could engage technical experts to undertake inspections of their buildings to determine whether the cladding and other materials used are appropriate and conform to relevant standards.
Regulatory and compliance professionals including builders, surveyors, technical assessors and building compliance officers also need to be aware of these risks, as do their professional indemnity insurers.
The consequences of using defective materials are potentially grave in terms of injury, fatality and rectification costs. Underwriters should be aware of those potential hazards when considering whether to accept a risk.